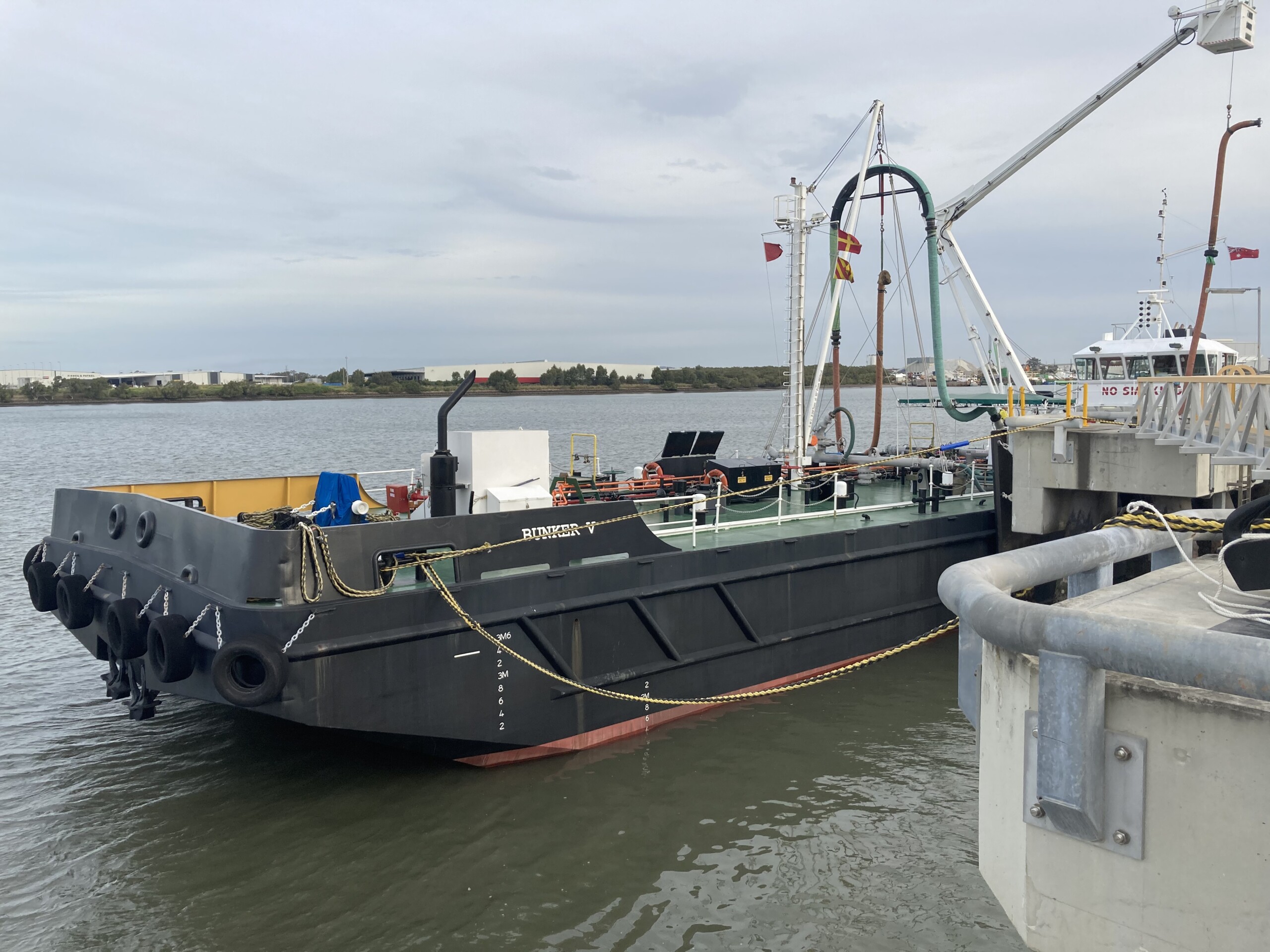
As one of Australia’s leading service providers in the hydrocarbon industry, Fuelfix & Tanks2Go offers numerous specialised functions related to Port Facility Management.
Our capability at the Brisbane Port has grown out of more than 10 years of providing fuel facility management services and continues to develop to support the evolving needs of our customers. Currently, we have a dedicated permanent team at the port to handle service and port works for many leading names like ATOM, BP Marine, PUMA Bitumen, Chevron Fuels and Origin (LPG). We work in a collaborative partnership with our customers to develop a solution and tailor services as per their unique requirements.
Our specialised support services include.
- Fuel unloading
- Product transfers
- General operations
- Laboratory sampling and quality testing
- Plant and equipment integrity testing and maintenance
- Provision of skilled labour-hire like Shore Officers, Bunker man, Wharf Watch Line Walker, Terminal Operator, Depot Operator, Electricians, fitters, boilermakers and Mechanics to name a few.
We also assist with overseeing and implementing ongoing maintenance, repairs and cleaning to all tanks, pumps, and pipes and associated equipment. Our industry-trained and experienced specialists undertake practices that are designed to put safety first. Adherence to all Safety and Environmental regulations is ensured with continuous training and instruction for all our staff. They are extensively trained in HSSE and understand the standard operating process and procedures like risk management and mitigation, incident reporting, work permitting and JSA safety and risk analysis principals. Our experience in port operations and logistics, backed by the ability of the wider Fuelfix group, ensures we deliver truly integrated solutions.
Why Fuelfix?
✔ Ongoing Support
We have a country-wide network of trained and trade qualified professionals. So, that means quick response time for your business and reduced downtime. Typically, a routine maintenance schedule is recommended with regular maintenance intervals set to minimize breakdowns. Fuelfix specializes in this area and can assist with the determination of interval here based on the varying factors of the installation and infrastructure.
✔ Safety
At Fuelfix, we are alert about occupational health & safety, environmental and corporate awareness issues. We have developed LEARNSafe, an in-house Health, Safety, Environment, and Quality (HSEQ) management system. This program provides policies and initiative to protect staff, clients, equipment and the environment.
✔ Quality
Fuelfix provides an internal Quality Assurance system on all products and services supplied. This system includes numerous checks, policies and procedures to ensure only the best products are supplied to the end-user. As part of this process, Fuelfix only deals with long term, reputable suppliers and contractors, to ensure maximum results and minimal downtime for clients.
✔ Productivity
Our team of experts have developed best practices, processes and policies which improve productivity and efficiency. Field technicians are constantly measured on productivity and this is reported weekly to senior management (and to clients where required). Within the business, the productivity of trade’s staff is measured and recorded on weekly productivity reports which are sent to senior management for review. Currently, the East Coast Fuelfix team averages 85-95% productivity per month, which is in line with company best practice.
If you would like to talk to one of our experts to discuss how we can tailor a solution for your business, call 1300 734 364 or contact us.