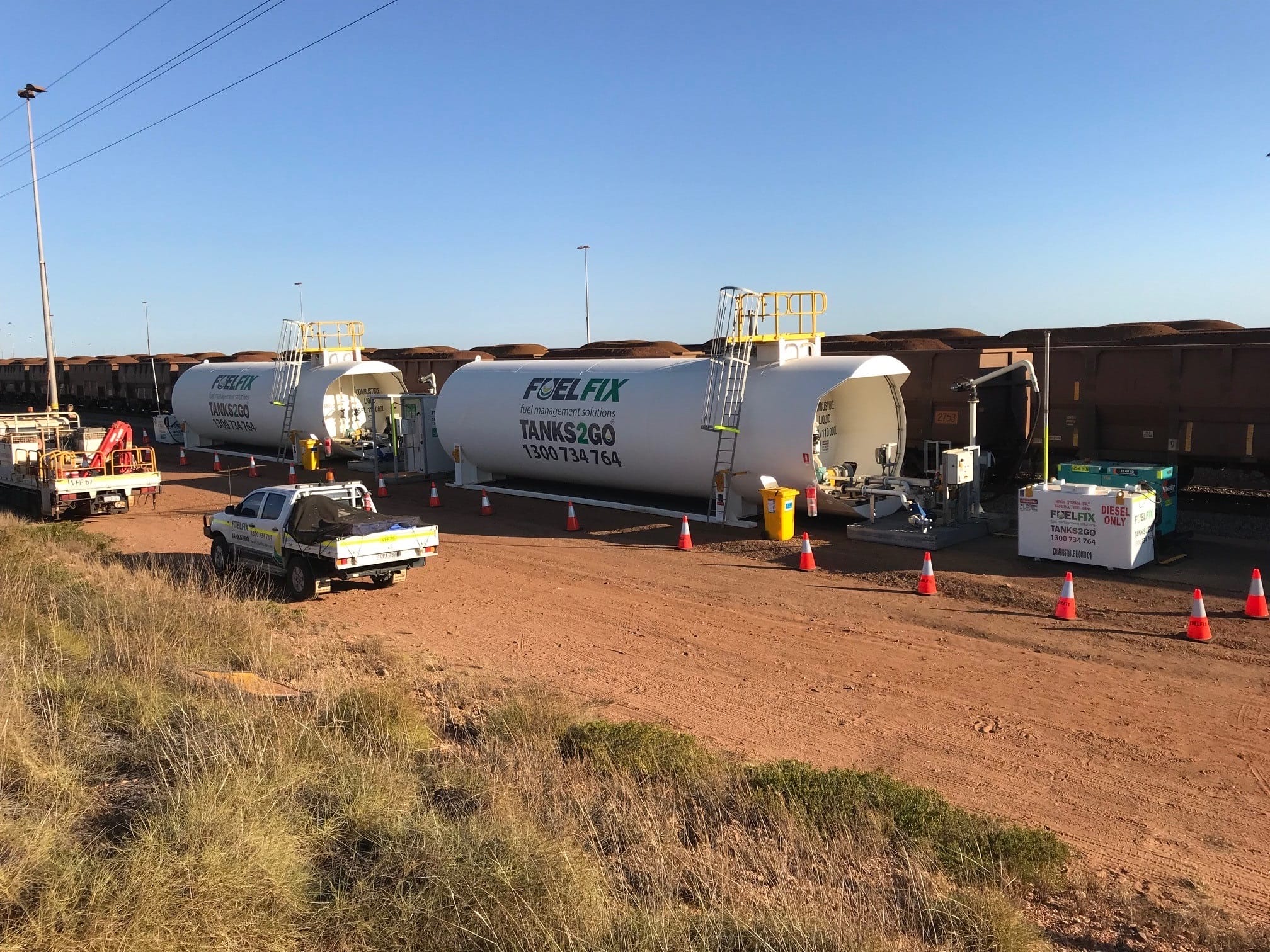
Companies today are under immense pressure to maintain top-quartile operational performance. This is important not only to stay competitive but also to establish themselves as industry leaders. Therefore, running equipment optimally cannot be neglected. Maximising equipment uptime means higher production rates, extended life expectancy of your equipment and lower risk of unplanned and emergency downtime.
An overwhelming 82% of companies have experienced at least one unplanned downtime incident over the past three years. Most have suffered two or more. source (1)
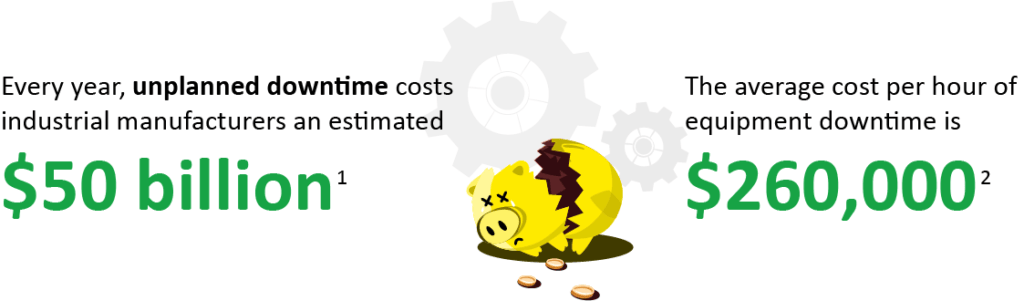
Here are 7 mistakes to avoid so that you can maximise your fuel equipment uptime like a pro!
1. Not undertaking a compliance audit
A site compliance audit is the fastest and most effective step you can take to reduce downtime in the future. A compliance audit will highlight problems and solutions so that you’re better prepared.
The key factors considered during a compliance audit are visual checks on all components of the fuel system, checking pressure testing records, ensuring calibration verification, general housekeeping and functional testing. More extensive audits can include detailed internal and external checks of fuel tank shells, thorough statutory compliance checks and proactive replacement of key parts.
2. Not calculating the cost of downtime
Not calculating the true cost of downtime is one of the biggest mistakes that companies make. A holistic approach in calculating downtime includes the loss in staff productivity, loss in production of actual goods, number of man-hours devoted to rescheduling, the unexpected costs of repairing equipment and damage to the overall reputation of the company. Downtime should always be calculated into a dollar figure. This combined with a proactive culture is crucial because it will help focus equipment improvement efforts and provide strong supply assurance to your customers and other stakeholders.
3. Ignoring critical spares
Your equipment can be made up of hundreds of individual parts manufactured by factories around the world. And the availability of these parts is critical to success; not having ready access to them is setting a business up for failure. Hence finding the right partner who can manage the supply of your critical spares and provide first class fuel equipment knowledge is essential in keeping operations running.
4. Not sticking to a preventive maintenance schedule
Gone are the days of the ‘run it till it breaks’ approach. To maintain a healthy production environment, it is vital that you keep a tab on your equipment and systems. And it is crucial to diagnose issues before they cause losses.
Preventive maintenance is favoured by 80% of maintenance personnel as part of a multi-faceted maintenance strategy (source)
Equipment cannot last forever, but a sound maintenance schedule will increase its life, reduce the cost of maintenance, improve utilization and ensure fewer unplanned downtime events. Additionally, it is important to monitor your equipment before and after use for any possible wear and tear or any abnormal vibrations or heat.
Read our article about the need of scheduled servicing and preventive maintenance program for fuel tanks.
An integrated approach of regular inspections and prompt attention to necessary repairs can also help protect the environment and enhance safety.
Machinery that is designed properly, installed, and maintained with precision can minimize the risk of environmental damage, reduce energy emissions (reduced power consumption, waste, and scrap), and reduce health and safety risks to operational and maintenance workers.
Preventive maintenance is part of Fuelfix & Tanks2Go Go-Greener initiative to reduce the impact of diesel fuel use on the environment and limit operating costs. Fuelfix & Tanks2Go Go-Greener range offers our customers options to reduce their greenhouse emissions and make better choices to commit to environmental sustainability standards.
5. Taking the one-size-fits-all approach
There is no magic remedy to fix equipment downtime. Every business needs to have a tailored preventive maintenance program as per their unique requirements.
30% of maintenance activities are carried out too frequently.
The tasks you have planned for your equipment may not be entirely necessary. (source)
You need an expert to factor in the variables relevant to your environment such as identifying the truly critical components, typical operating conditions and the optimum frequency of inspections – all aimed at keeping the systems operating efficiently and within legislative requirements.
6. Thinking reactively rather than proactively
Proactive thinking will ensure you adopt the systems and habits needed to stop problems before they occur. Adopting a proactive approach and culture will play a major role in the success of any preventive maintenance.
7. Not having a partner, you can trust
Undoubtedly, optimising equipment uptime is hard work, but you do not have to do it alone. With the right partner, keeping fuel equipment running can be a hassle-free process.
At Fuelfix & Tanks2Go, our focus is to help you achieve your goals by customising a solution to fit the unique needs of your business. We will design a preventive maintenance program to keep your system operating both efficiently and within legislative requirements. And with locations across Australia, we provide local support with a quick response time for your business.